
He says tie straps used to secure the harnesses to the frame are usually pulled too tightly, or it may be the vibration alone, but there are usually telltale signs to look for when visually inspecting the harness. Most good technicians understand troubleshooting and repair processes, but they don’t always follow them.” – Toy DeGroot, Bison TransportĮxperience has taught DeGroot that wiring problems are more likely to be rub-throughs than corroded connectors. If there’s no power there, you know the problem is between the source and that connector. If there’s power there, you know the failure is between that and the load. If that’s good, check a connector at some midpoint in the circuit. If the light is good, but there’s no power, check the fuse or the source of the power to ensure you have voltage there. “Then work toward isolating the problem by breaking the circuit into smaller chunks.” “Start by determining whether you have no voltage at the light, for example, or a failed light,” he recommends. DeGroot advises his technicians to start with basic elements of any circuit: the source, a switch or control, the load, and a ground.
#Wire connector how to
“They can fall into the trap of saying, ‘I’ve seen that problem before, I know how to fix it,’ but without doing proper diagnostics, things can be overlooked.”Įven if a technician has done a certain repair a dozen times, there’s always a chance the problem is not what it appears to be. “Most good technicians understand troubleshooting and repair processes, but they don’t always follow them,” DeGroot says. It’s not necessarily bad, he says, but sometimes a problem isn’t what it appears to be. Bison Transport’s manager of technical training and product development, Tony DeGroot, calls it technician discretion. Many experienced technicians develop their own way of doing things over the years, of course. Semi-skilled technicians can do more harm than good with improper electrical repairs. Electrical troubles don’t always present in a way that intuitively leads to the root of the problem. If nothing else, this bring some consistency to the process.
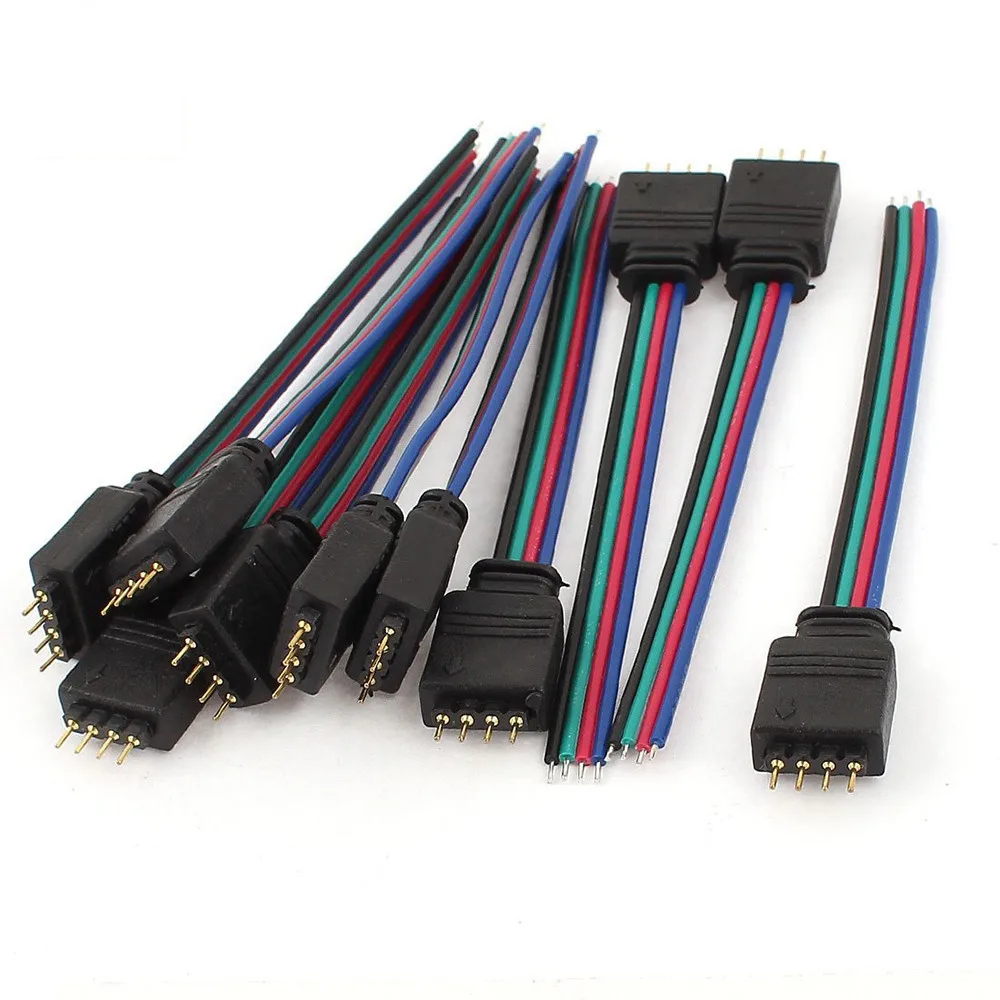
These provide clearly defined diagnostic steps to determine a problem, and they outline correct repair procedures. Some of Canada’s top fleets have learned from experience the true cost of improper diagnostics and repairs, and have implemented rigorous procedures and standards for electrical repairs.

Because of the complex nature of modern electrical and electronic systems, unskilled, lazy, or even over-confidant technicians can waste tons of time and money chasing ghosts or replacing perfectly good parts. Electrics is one aspect of truck repair where a little bit of knowledge can be more harmful than helpful.
